We Strive To Create The Most Precise And Consistent Casings Available Today
The steps below show Peterson Cartridge's brass cartridge casing manufacturing process from the original brass manufacturer and their cupping process through the final mouth and neck anneal. If you have any questions about our process or want to learn more, please contact us.
1. Brass Manufacturing
Each cartridge casing begins its life as a brass “coil” formed when copper and zinc, along with a few trace elements, are combined to form brass. The particular type of brass our industry uses to form casings is called C260, or “Cartridge Brass”. The picture to the right shows a few brass and copper coils ready to move onto the next step of their manufacturing processes.
Photo courtesy of Aurubis
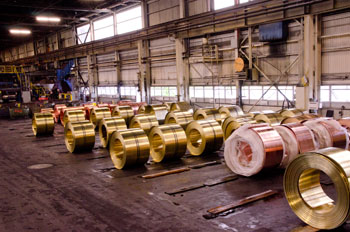
2. Cupping Process
The wide brass coils are then slit into narrower brass coils ready to enter the cupping presses. In the picture to the right, you can see a coil of brass feeding through a cupping press. The cupping press is usually a multi-punch-per-stroke press. This allows the manufacturer to produce cups at a very high rate of speed. After cupping, the cups are captured in bins, and the scrap brass which is left over is then melted back down to form more coils.
Photo courtesy of Aurubis
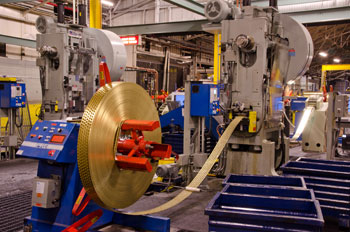
3. Finished Cups
Cups are very stout, and are a little wider than they are deep. Notice the ridges on top of the cup. As the cup is drawn into a casing, these ridges become more pronounced.
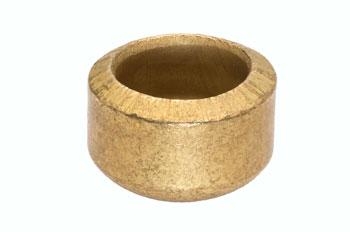
4. 1st Draw
This is what a cup looks like after passing through the first of three draw presses. The cup is now a little taller, and considerably narrower. The cup then has to be annealed, or heated, to relax the grain structure of the metal enough to continue elongation. The casing also has to be washed prior to being put through the next draw process.

5. 2nd Draw
The cup has now passed through the second of three draw presses. The cup is now much deeper than it is wide, and is starting to look like a close-ended tube. As with the first draw, the cup will need to be annealed and cleaned again prior to further elongation.
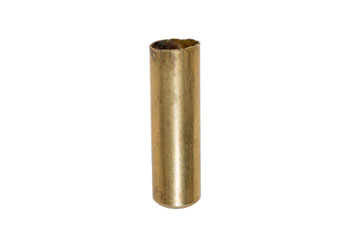
6. 3rd Draw
The cup has now reached its total elongated length, and is now considered a casing. Notice how uneven the top of the casing is. This is partially due to the grain structure in the side walls of the cup, as well as cup side wall thickness variations. It should be noted that it is not usual to see a casing in this form, as it would have been pinch trimmed prior to exiting the third draw press.
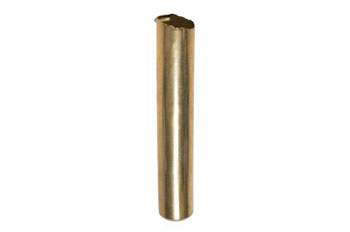
7. Pinch Trim
Here we have displayed the ring of brass trimmed off the top of the tube in the last step. “Pinching” off the extra material at the top of the tube provides us a perfectly trimmed-to-length tube ready for the next forming operation. The tube also has to be washed prior to being advanced onto the next step of the forming process.
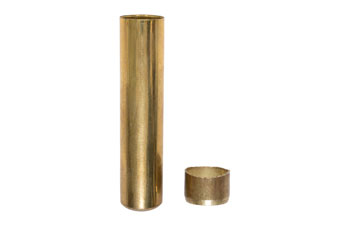
8. Forming The Primer Pocket & Heading The Case
The forming of the primer pocket and applying the headstamp to the bottom of the casing are actually two separate steps. First, the casing is basically “rammed” against the pocketing tool. This step creates the primer pocket in the bottom of the casing where the primer is seated. Next the pocketed casing progresses to the bunter which flattens the bottom of the casing and applies our headstamp, or “heads” the case, by again “ramming” the case against the raised letters and numbers of the bunter. The casing also has to be washed prior to being advanced onto the next step of the forming process.
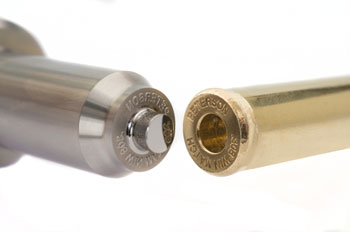
9. Cutting The Extraction Groove
Next, the pocketed and headed casing has its extraction groove cut. This operation is very similar to a horizontal lathe. The casing is clamped on a spindle and rotated at a high speed while the profile cutter is pressed against it. The rotation of the casing in combination with the contact of the profile cutter creates the casing’s extraction groove. Prior to advancing onto the next process, the body of the casing has to be annealed again to relax the grain structure of the metal.
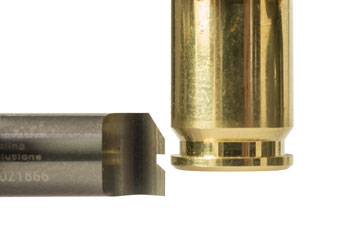
10. 1st Taper
The casing displayed here has gone through the first taper press. As you can see, it is starting to show the profile of the neck and mouth. The casing has also begun to receive its body taper.
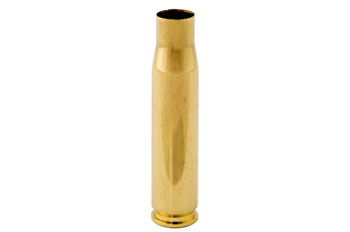
11. 2nd Taper
The casing has now gone through the second press inside the taper operation. As you can see, the body, shoulder, and neck continue being refined to their final dimensions.

12. 3rd Taper
Now the casing has been tapered to its final body, neck, and mouth dimensions. However, the overall casing length is still too long and does not have a flash hole yet. Prior to advancing onto the next process, the casing has to be washed again.
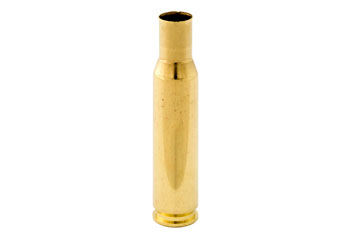
13. Trim-to-Length
The casing now has to be trimmed to length. The use of specially designed carbide cutters, combined with frequent cutter replacement, is what prevents the creation of burrs on the inside and outside of the casing mouth.
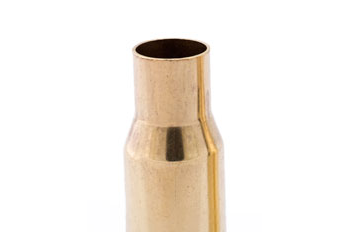
14. Punching the flash hole
Here we have a casing after the flash hole is punched. The precision used to punch the flash hole has a tremendous effect on the performance of the finished casing. A high-quality casing will have a precisely punched flash hole which is free of burrs and tearing. It is also important that the flash hole is uniform in size from casing to casing.
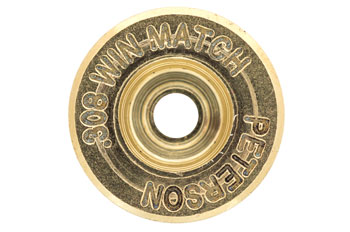
15. Mouth and Neck Anneal
To the right we have displayed a casing after it has received its mouth and neck anneal. Annealing the mouth and neck of each casing is important to ensure the casing “grabs” the projectile correctly and releases the projectile uniformly when the casing is fired. Our machinery utilizes induction annealing rather than flame annealing. Unlike flame annealing, while using induction annealing, we are able to control the temperature, applied to each casing, to the degree.
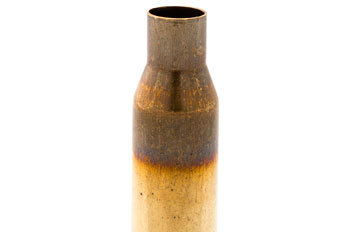
16. The Washes
We thought it necessary to specifically mention our wash processes. As you can imagine, we don’t use a regular soap to clean our casings between processes. Our wash chemicals are a combination of acids, detergents, and anti-tarnish compounds which effectively remove the lubricant used in our draw processes as well as clean off any tarnish which might have developed during our manufacturing operation. Our wash chemicals and processes do all of this while still ensuring the casings you receive have a beautiful polished-brass luster.
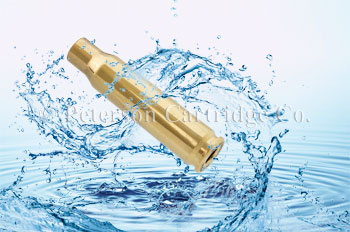